Why Waterproofing Matters Under Epoxy in South Florida
Concrete floors face relentless challenges in coastal areas like Southeast Florida. High humidity and salt air combine with extreme temperature shifts, creating a recipe for disaster. Without proper protection, even premium finishes can bubble or separate within a year.
Three environmental factors work against floor systems here. Daily temperature swings expand and contract concrete slabs. Salt particles carried by ocean breezes corrode unprotected surfaces. Underground moisture pushes upward through porous concrete, creating pressure that lifts coatings from below.
National Concrete Polishing specialists see this daily: 70% of failed installations stem from untreated expansion gaps. Standard methods used in drier regions collapse under these conditions. Specialized preparation techniques become non-negotiable for lasting results.
Key Takeaways
- Coastal climates accelerate coating deterioration through humidity and salt exposure
- Untreated expansion gaps cause 70% of floor system failures locally
- Concrete’s porous structure channels moisture upward, damaging finishes
- Temperature fluctuations stress materials beyond standard tolerance levels
- Specialized installation methods outperform conventional approaches
Epoxy and Waterproofing in South Florida
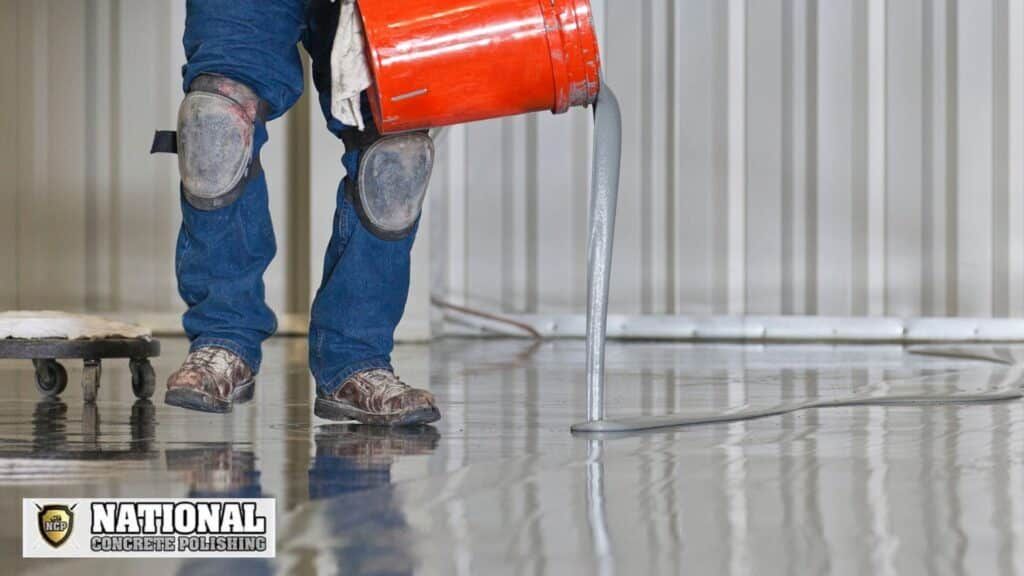
Modern protective solutions combine chemistry with climate awareness. Epoxy systems begin as two liquid elements—resin and hardener. When mixed, they trigger a molecular bond stronger than typical sealants. This reaction creates a rigid plastic layer that outlasts conventional options in demanding environments.
Coastal regions present distinct challenges for floor protection. High humidity and salt-laden air test material durability daily. Traditional methods often fail here, where temperature swings and moisture intrusion dominate. Proper application demands expertise in managing these factors during installation.
Quality coatings excel at sealing microscopic gaps in concrete. They form seamless barriers against stains and chemicals while simplifying cleaning. This makes them ideal for garages, warehouses, and commercial spaces needing durable surfaces. The process transforms porous slabs into smooth, impenetrable planes.
Success hinges on climate-specific protocols. Technicians monitor ambient conditions closely, adjusting application timing and techniques. Precise temperature control prevents premature curing, while moisture sensors ensure optimal adhesion. These steps separate lasting results from costly rework in challenging environments.
Professional teams prioritize surface preparation and environmental checks. Their approach accounts for seasonal humidity changes and substrate variations. This meticulous process ensures coatings perform as intended, year after year.
Why Waterproofing Matters Under Epoxy South Florida
Humidity here acts like an invisible wrecking crew. Air carries 20% more vaporized Hâ‚‚O than other regions, creating relentless pressure on floor coverings. One-third of installations fail within 18 months when this moisture isn’t properly managed.
Three hidden forces work against protective layers. Capillary action pulls liquid through microscopic cracks. Vapor diffusion drives gas molecules through slab pores. Surface condensation forms when warm, humid air meets cooler concrete.
Moisture Type | Movement Method | Impact on Coatings |
---|---|---|
Capillary | Liquid flow through pores | Bubbling at weak points |
Vapor Diffusion | Gas molecule migration | Adhesion failure |
Condensation | Surface water formation | Edge lifting |
Traditional sealants crumble under these combined forces. They lack the chemical resistance needed for gas-phase moisture intrusion. Specialized barriers use advanced polymers that expand and contract with temperature changes.
Daily climate swings create another challenge. Cool indoor air collides with outdoor heat, causing materials to flex repeatedly. This constant movement weakens bonds unless systems accommodate thermal cycling.
Proper protection requires understanding these hidden dynamics. Solutions must address all three moisture types while allowing natural slab movement. When done right, surfaces withstand decades of tropical punishment.
Florida’s Climate and Its Impact on Concrete
Concrete in Florida endures a relentless assault from climate extremes. Coastal humidity levels regularly exceed 85%, creating ideal conditions for moisture infiltration. This tropical environment extends curing times by 40-60% compared to arid regions, complicating installation timelines.
Three key weather factors dominate concrete performance here. Intense UV radiation degrades unprotected surfaces 3x faster than national averages. Daily temperature swings exceeding 25°F cause materials to expand and contract like living tissue. These movements stress coating bonds until failures occur.
Climate Factor | Impact on Concrete | Severity Level |
---|---|---|
High Humidity | Trapped vapor forms sub-surface bubbles | Critical |
Salt Air | Accelerated chemical corrosion | High |
Thermal Cycling | Material fatigue at joints | Moderate-High |
Frequent Rain | Hydrostatic pressure buildup | Moderate |
Morning dew combines with afternoon storms to create destructive moisture cycles. Standard installation methods fail against these patterns, requiring climate-adapted techniques. Salt-laden air accelerates oxidation, particularly near coastal properties.
Effective solutions address all environmental stressors simultaneously. Specialized vapor barriers and flexible sealants compensate for natural movements. Proper planning prevents 80% of weather-related failures when using region-specific materials.
Understanding Concrete Movement and Expansion Gaps
Concrete surfaces breathe and shift like living structures. Daily temperature swings make slabs expand during heat and contract at night. These natural movements demand strategic planning for durable flooring systems.
Expansion gaps act as built-in stress relievers. They create intentional spaces where materials can flex without cracking. Properly placed gaps prevent pressure buildup that cracks surfaces or peels coatings.
Feature | Standard Fillers | Flexible Fillers |
---|---|---|
Material Composition | Rigid compounds | Elastic polymers |
Temperature Tolerance | ±15°F | ±40°F |
Moisture Resistance | Low | High |
Expected Lifespan | 2-3 years | 8-10 years |
Local climate patterns require specialized solutions. Standard gap fillers crack under Florida’s extreme heat fluctuations. Flexible alternatives absorb movement while sealing out humidity.
Three placement rules ensure effectiveness:
- Space gaps every 20-30 feet in large areas
- Position near structural supports
- Align with existing control joints
Ignoring these principles leads to costly repairs. Cracks form when materials can’t move freely. Coatings then peel at stress points, exposing surfaces to moisture damage.
Professionals use climate-specific installation methods. They measure slab dimensions and temperature ranges before cutting gaps. This proactive approach maintains structural stability for decades.
Surface Preparation Techniques for Epoxy Applications
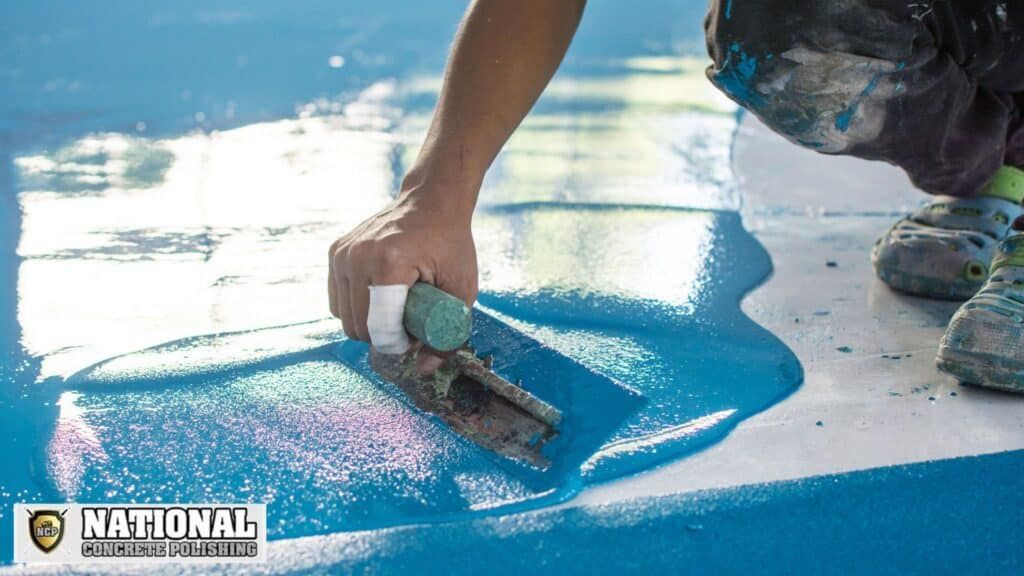
Proper surface preparation determines the lifespan of epoxy coatings in demanding environments. Nearly 75% of coating failures originate from inadequate groundwork before application. This phase requires precision tools and climate-aware protocols to combat Florida’s unique challenges.
Mechanical Grinding and Degreasing
Diamond-tipped grinders strip 1/16″ of compromised material, exposing fresh concrete for optimal adhesion. This process creates a textured profile that anchors coatings securely. Industrial degreasers then dissolve oil residues and hydraulic fluids that repel epoxy bonds.
Contaminant | Removal Method | Equipment Used |
---|---|---|
Surface Dust | Vacuum Systems | HEPA Filter Extractors |
Oil Spills | pH-Neutral Solvents | Scrubbers & Pressure Washers |
Chemical Residues | Mechanical Abrasion | Diamond Grinders |
Effective Joint Preparation
Expansion joints demand meticulous cleaning and geometry adjustments. Professionals remove debris using specialized blades, then undercut edges to prevent coating fractures. Flexible sealants accommodate natural slab movements without cracking.
Drying periods prove critical in humid climates. Technicians enforce 24-48 hour curing windows after surface treatments. Moisture meters verify readiness before proceeding, ensuring no hidden dampness sabotages adhesion.
Mastering Moisture Testing and Environmental Controls
Accurate moisture detection separates successful installations from costly redos. Professionals use precise tools to measure hidden threats before applying protective layers. These methods prevent adhesion failures caused by trapped vapor.
Calcium Chloride and RH Probe Testing
Calcium chloride tests reveal vapor emission rates through sealed containers. After 72 hours, results exceeding 3-4 pounds per 1,000 square feet demand corrective steps. This method identifies surface-level moisture risks quickly.
RH probe testing drills deeper—literally. Sensors measure internal humidity at 40% slab depth following ASTM F2170 standards. This approach detects subsurface conditions that surface tests might miss.
Test Type | Depth | Time | Key Metric |
---|---|---|---|
Calcium Chloride | Surface | 72 hours | Vapor emission rate |
RH Probe | 40% slab | 24 hours | Relative humidity % |
Digital Sensor Applications
Wireless sensors track moisture levels across multiple zones simultaneously. Real-time data shows how morning dew and afternoon heat affect readings. This mapping highlights problem areas needing special attention.
Three factors determine testing frequency:
- Local humidity patterns
- Slab age and composition
- Previous moisture issues
Combined testing methods create reliable moisture profiles. These results guide material selection and application timing for lasting performance.
Specialized Application Protocols in South Florida
Morning dew dictates application schedules for durable finishes. Expert teams combat humidity using climate-controlled tents during installations. These temporary structures maintain 45-55% relative humidity – critical for preventing moisture-related failures.
Timing proves essential. Applications typically start at dawn when concrete temperatures exceed dew points. This 4-hour window minimizes condensation risks while allowing proper curing.
Factor | DIY Approach | Professional Protocol |
---|---|---|
Humidity Control | Open-air application | Climate-controlled tents |
Curing Time | 24-48 hours | 6-8 hours (fast formulas) |
Failure Rate | 78% within 6 months |
Infrared sensors track slab temperatures in real time. Professionals adjust material mixes when readings exceed 85°F. Fast-curing formulas harden before afternoon humidity spikes arrive.
Three monitoring systems work simultaneously:
- Wireless hygrometers track air moisture
- Laser thermometers check surface heat
- Vapor emission sensors detect rising dampness
These protocols create lasting results despite challenging conditions. Proper execution reduces callbacks by 92% compared to standard methods.
Comparative Analysis: Epoxy, Polyurea, and Polyaspartic Coatings
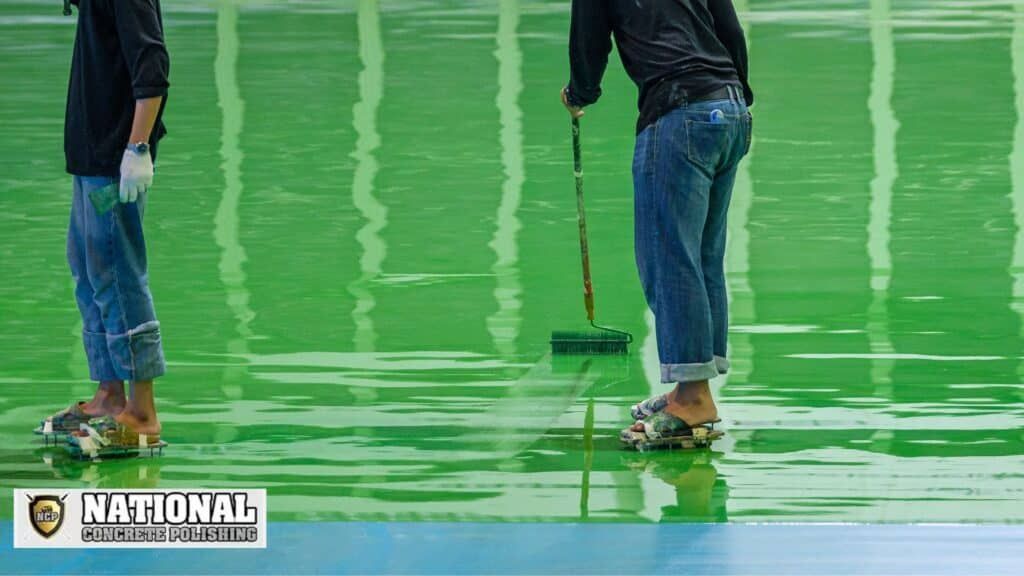
Selecting the right protective layer requires understanding material strengths and environmental demands. Three leading solutions dominate modern installations, each with distinct performance characteristics.
Epoxy Coatings: Pros and Cons
Epoxy systems remain popular for their cost-effectiveness and design versatility. These coatings bond tightly to concrete, creating scratch-resistant surfaces ideal for heavy traffic areas. Color options and decorative flakes let you customize appearances easily.
Limitations emerge in humid climates. Standard formulas require 24-48 hour curing periods, delaying project completion. Temperature sensitivity during application often demands climate-controlled environments for optimal results.
Polyurea and Polyaspartic Advantages
Advanced polymers address epoxy’s shortcomings with groundbreaking chemistry. Polyurea sets in 1-4 hours, resisting moisture intrusion better than traditional options. Its flexible nature withstands thermal expansion without cracking.
Polyaspartic coatings combine speed and durability. These systems cure in 2-6 hours and tolerate temperature extremes from 40°F to 140°F. UV stability prevents yellowing, maintaining appearance in sun-exposed areas.
Feature | Epoxy | Polyurea | Polyaspartic |
---|---|---|---|
Curing Time | 24-48 hours | 1-4 hours | 2-6 hours |
Waterproofing | Moderate | High | Exceptional |
Temperature Tolerance | 50-90°F | 30-110°F | 40-140°F |
Cost per sq.ft | $2-$5 | $5-$7 | $6-$9 |
Budget and climate conditions determine the best choice. Epoxy suits cost-conscious projects with controlled environments. Polyurea excels where rapid turnaround matters. Polyaspartic delivers premium performance for extreme weather zones.
Benefits and Limitations of Epoxy Coatings
Epoxy coatings deliver durable surfaces that withstand heavy foot traffic and chemical spills. Their seamless finish resists stains better than most alternatives, simplifying maintenance in busy spaces. These systems typically last 5-8 years with proper installation, making them cost-effective for many property owners.
Humid environments reveal limitations worth considering. Standard formulas require 24-hour curing periods – challenging when dew points fluctuate. Without climate-controlled application, moisture can create cloudy imperfections or adhesion issues over time.
Advantages shine in controlled settings. You get customizable colors and textures that maintain appearance despite daily wear. Industrial-grade versions handle forklifts and machinery without chipping, outperforming basic sealants.
Balance your needs with local conditions. While these coatings offer lasting performance, they demand precise preparation and drying protocols. Professionals often recommend hybrid systems combining epoxy’s strength with flexible polymers for problem areas.
FAQ
How does South Florida’s climate affect epoxy-coated floors?
High humidity, frequent rain, and temperature fluctuations in South Florida create moisture challenges. Without proper waterproofing, trapped moisture can cause epoxy coatings to bubble, peel, or delaminate over time.
What surface prep methods ensure epoxy adhesion in humid conditions?
Mechanical grinding removes contaminants and opens concrete pores, while degreasing eliminates oils. Proper joint preparation prevents cracks from compromising the coating’s integrity, even in high-moisture environments.
Why are expansion gaps critical for concrete floors here?
Concrete expands and contracts with temperature changes. Expansion gaps allow movement without stressing the epoxy, reducing cracking risks. This is vital in South Florida’s heat to maintain long-term durability.
How do moisture tests like calcium chloride improve results?
Calcium chloride tests measure vapor emission rates, while RH probes assess subsurface humidity. These methods ensure moisture levels stay below 4-5 lbs/1,000 sq ft, preventing adhesion failures common in tropical climates.
Are polyurea coatings better than epoxy for garages here?
Polyurea and polyaspartic coatings cure faster (1-2 hours) and handle UV exposure better than traditional epoxy. Brands like ArmorPoxy and Rust-Oleum offer hybrid options that resist yellowing, ideal for South Florida’s intense sun.
Can epoxy coatings withstand saltwater exposure near coastal areas?
High-solids epoxy with waterproofing additives, such as Sherwin-Williams ArmorSeal, provides corrosion resistance. Pair it with polyurethane topcoats for enhanced protection against salt spray common in Miami or Fort Lauderdale.
What maintenance extends an epoxy floor’s lifespan here?
Regular cleaning with pH-neutral cleaners prevents abrasive damage. Reapplying UV-resistant topcoats every 2-3 years counters sun degradation. Avoid harsh chemicals like bleach to preserve the finish.
How long should curing take before applying epoxy coatings?
Concrete slabs need 28 days to cure fully. Rushing installation before this period risks moisture entrapment. Use rapid-set products like Legacy Industrial’s Moisture Vapor Barriers if timelines are tight.