Understand What is the Concrete Polishing Diamond Grit Sequence for Your Floors
Did you know floors polished with precision can withstand heavy foot traffic for over 25 years? This durability stems from one critical factor: strategic abrasive progression . Without the right approach, surfaces lose their luster within months.
Professionals start with coarse tools to eliminate imperfections, then gradually refine surfaces. Coarser abrasives (like 30-40 grit) strip away old coatings and level uneven areas. Mid-range options (80-150 grit) smooth edges and prepare for final treatments.
Higher grit levels (800+) create that coveted glass-like finish. Skipping steps or rushing this progression leaves visible scratches and weakens the surface. That’s why experts like National Concrete Polishing in South Florida follow meticulous protocols—call them at +1 877-661-7562 to see the difference.
Key Takeaways
- Proper abrasive progression ensures durability and aesthetic appeal
- Initial coarse grinding removes flaws and creates a uniform base
- Each stage eliminates scratches from the previous step
- Final high-grit polishing achieves reflective, easy-to-maintain surfaces
- Expert techniques prevent costly rework and extend floor lifespan
Overview of Polished Concrete: Benefits & Considerations
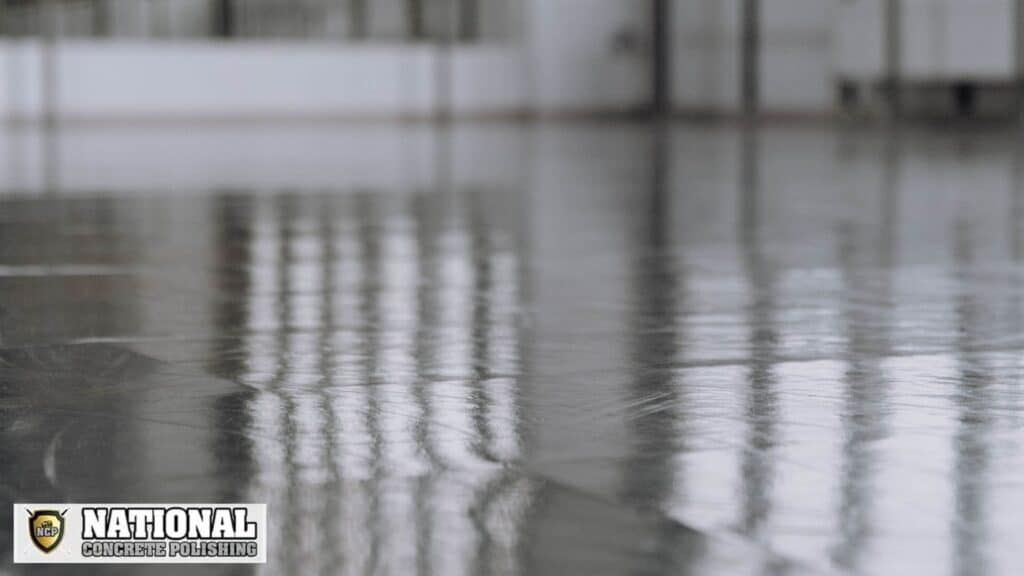
South Florida properties thrive with surfaces that blend beauty and resilience. Polished concrete delivers both , transforming ordinary slabs into high-performance assets. Let’s explore why this flooring solution dominates modern design.
Why Choose Polished Concrete for Your Space
Durability meets style here. These floors withstand decades of heavy use without cracking or fading. Unlike carpet or tile, they resist stains and allergens with simple damp mopping.
Cost savings add up quickly. Initial installation often costs less than traditional options, and you’ll never budget for replacements. The reflective finish cuts lighting costs by up to 30%—ideal for sun-drenched Florida spaces.
Flooring Type | Lifetime Cost | Maintenance Effort | Lifespan |
---|---|---|---|
Polished Concrete | $4.50/sqft | Low | 25+ years |
Carpet | $12.80/sqft | High | 5-7 years |
Tile | $9.20/sqft | Medium | 10-15 years |
National Concrete Polishing: South Florida Experts
Local conditions demand specialized knowledge. Humidity, salt air, and substrate variations all affect polishing results. Our team at +1 877-661-7562 brings 15 years’ experience adapting techniques for coastal properties.
We’ve perfected eco-friendly processes that enhance existing slabs. No demolition waste. No toxic cleaners. Just stunning floors that perform year after year in Miami heat and Key West downpours.
Demystifying what is the concrete polishing diamond grit sequence
Proper surface treatment transforms ordinary slabs into architectural masterpieces. Strategic abrasive selection determines whether floors endure decades of use or show wear within months. Let’s explore how professionals systematically refine surfaces.
Understanding Diamond Grit Levels and Their Roles
Coarse abrasives (30-100 grit) act like heavy-duty sandpaper. They strip old sealants, flatten uneven patches, and expose fresh material. This stage removes deep stains and creates a uniform base for subsequent steps.
Medium-grade tools (100-400 grit) refine textures. These eliminate scratches from initial grinding while preparing for densification. Skipping this phase risks trapping imperfections under glossy finishes.
Grit Range | Primary Purpose | Scratch Size Reduction |
---|---|---|
30-100 | Aggressive material removal | 80-90% |
100-400 | Surface refinement | 95-97% |
800-3000 | Optical clarity enhancement | 99%+ |
How the Grit Sequence Enhances Floor Durability and Appearance
Each progressive stage minimizes scratch visibility. Fine abrasives (800-3000 grit) activate chemical reactions that densify surfaces. This process creates stain-resistant finishes that repel spills better than untreated slabs.
Proper sequencing locks in structural integrity. Floors polished through methodical grit progression withstand forklifts, foot traffic, and UV exposure without cracking. The result? Spaces that maintain their mirror-like sheen for years with basic care.
Step-by-Step Guide to Polishing Your Concrete Floors
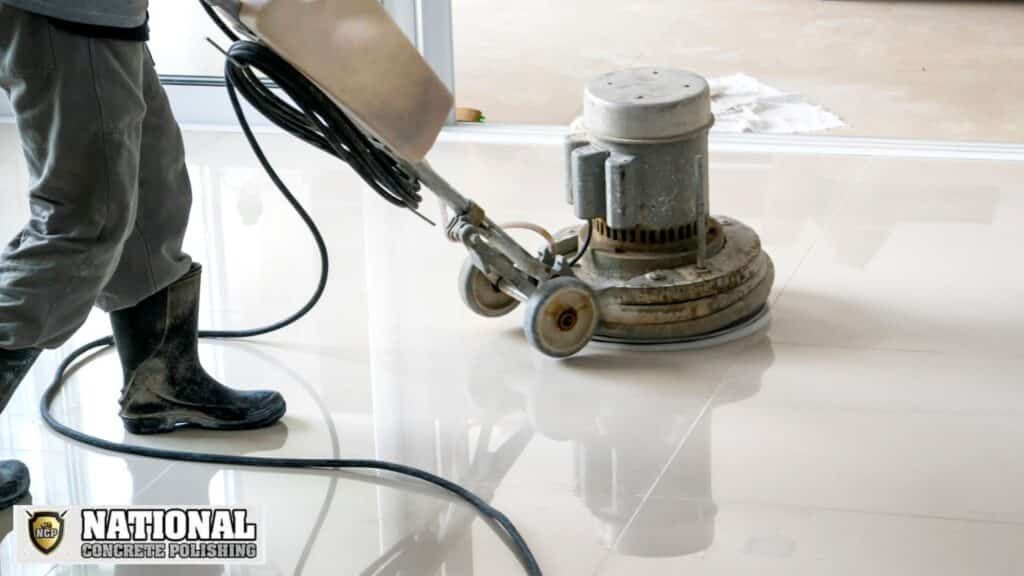
Achieving mirror-like floors requires following a systematic approach. Proper execution at each phase ensures lasting results and prevents costly mistakes. Let’s break down the stages professionals use to transform ordinary slabs into showstopping surfaces.
Preparation: Cleaning, Repair, and Surface Evaluation
Start by clearing debris and old adhesives. Use mechanical scrapers or eco-friendly solvents for stubborn residues. Inspect for cracks—fill them with polyurea compounds that bond tightly and prevent future spreading.
Test moisture levels and check for uneven areas. Address low spots with patching compounds to create a flat base. A clean, stable foundation is non-negotiable for flawless finishes.
Grinding, Densification, and Progressive Refinement
Begin with 30-40 grit tools to level the slab. This aggressive grinding removes imperfections and exposes fresh material. Move to 80 grit abrasives to smooth scratches, then 150 grit for finer refinement.
Apply liquid densifier immediately after grinding. The solution reacts with calcium hydroxide, forming ultra-hard calcium silicate hydrate. This chemical transformation strengthens the slab and enhances shine retention.
Grit Level | Primary Action | Time per 1,000 sqft |
---|---|---|
30-40 | Aggressive leveling | 3-4 hours |
80 | Scratch removal | 2-3 hours |
150 | Surface smoothing | 1.5-2 hours |
Final Polishing and Protective Sealing Techniques
Switch to 400+ grit tools for glossy finishes. Higher grits (800-3000) enhance reflectivity—ideal for commercial spaces wanting maximum light reflection. Work in circular motions to eliminate micro-scratches.
Apply penetrating sealers after polishing. These products repel stains without creating slippery films. Reapply every 2-3 years in high-traffic areas to maintain protection.
Most projects take 2-4 days. Factor in drying times between stages—rushing causes hazing or weak bonds.
Essential Equipment, Techniques & Maintenance Best Practices
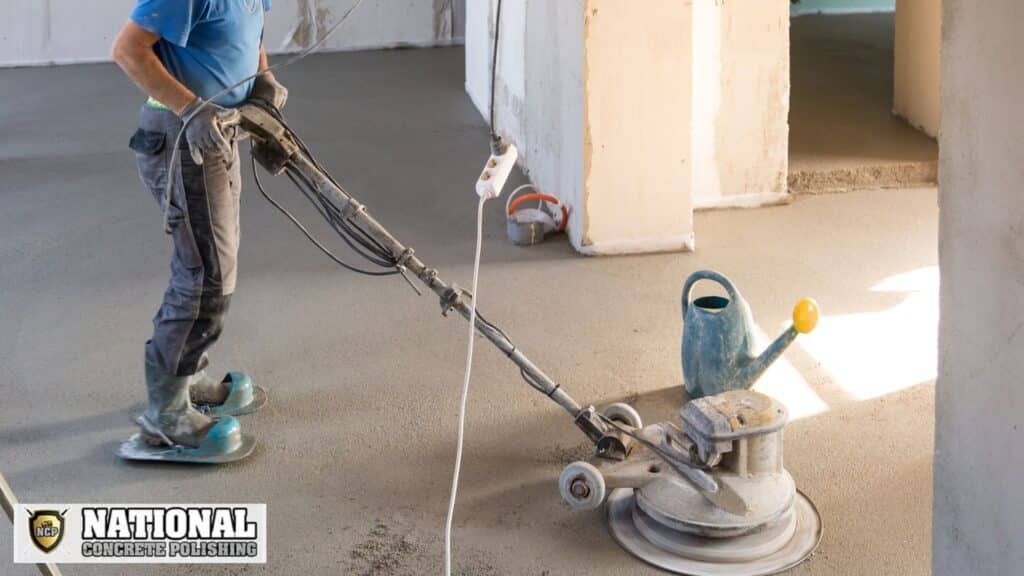
Quality results demand the right arsenal. Professional-grade tools streamline workflows while minimizing errors common with DIY approaches. Let’s explore how strategic investments in equipment and care routines preserve floors for decades.
Key Tools and Diamond Abrasives for a Professional Finish
Start with diamond grinders featuring interchangeable discs (30-400 grit). These handle heavy material removal and precise refinishing. Pair them with HEPA-filter vacuums to capture 99.97% of airborne particles during grinding.
Equipment Type | Purpose | Avg. Cost |
---|---|---|
Planetary Grinder | Initial surface leveling | $8,500+ |
Edge Grinder | Perimeter work | $2,200+ |
Burnisher | Final gloss enhancement | $1,800+ |
Concrete densifiers like lithium silicate hardeners penetrate pores, boosting scratch resistance. Apply them after 400-grit polishing for optimal absorption.
Modern Techniques, Cost-Effectiveness, and Ongoing Maintenance Tips
Rentals cost $300-$600 daily but lack precision settings. Owning equipment pays off after 5+ projects.
Preserve surfaces with:
- Daily dry mopping using microfiber pads
- pH-neutral cleaners (e.g., DailyKlean) for weekly deep cleans
- Reapplying sealers every 24-36 months in high-traffic zones
Avoid vinegar or ammonia-based products—they degrade protective coatings. Address spills within 30 minutes to prevent staining. With proper care, your floors maintain their luster through years of heavy use.
Conclusion
Transforming industrial slabs into elegant surfaces requires more than basic tools. Strategic abrasive progression creates floors combining resilience with visual appeal. Each stage in the refinement process builds upon the last, locking in structural integrity while enhancing light reflection.
While small DIY projects can yield decent results, professional execution guarantees lasting performance. Experts assess substrate conditions, select optimal grit sequences, and apply advanced densifiers. This approach prevents premature wear and maintains desired gloss levels through decades of use.
National Concrete Polishing masters these techniques for South Florida’s unique climate. Their team adapts methods for coastal humidity and high-traffic demands. Call +1 877-661-7562 to discuss customized solutions that protect against stains and salt air corrosion.
Investing in proper surface treatment pays dividends through reduced maintenance and replacement costs. You gain floors that withstand heavy use while elevating interior aesthetics. Partner with seasoned specialists to maximize your space’s potential.
FAQ
Why do you start with coarse diamond grits during polishing?
Coarse grits (like 40-80) remove imperfections, stains, and old coatings. This creates a flat surface for finer grits to build upon. Skipping steps risks uneven finishes or trapped damage.
How does chemical densification improve floor durability?
Densifiers like lithium silicate penetrate pores, reacting with calcium hydroxide to harden surfaces. This reduces dusting, boosts stain resistance, and supports higher gloss levels during polishing.
Can cracks in existing floors be fixed before polishing?
Yes. Epoxy fillers or polymer-modified cement repairs address cracks. Proper evaluation ensures structural integrity before grinding begins. Ignoring repairs leads to visible flaws post-polishing.
What equipment is essential for a DIY polished concrete project?
Rent a planetary grinder with diamond abrasives (metal-bonded for grinding, resin-bonded for refining). Use a vacuum to control dust and a burnisher for final gloss. Professional-grade tools yield consistent results.
How long does a polished concrete floor last with maintenance?
Properly sealed surfaces last 10+ years. Regular cleaning with pH-neutral cleaners and periodic reapplications of guard products prevent wear. Avoid harsh chemicals to maintain shine and stain resistance.
Does higher grit (like 1500-3000) make floors slippery?
Not if sealed correctly. High-grit polishing enhances reflectivity, but anti-slip additives in sealants or matte finishes balance safety. Discuss traffic needs with contractors like National Concrete Polishing for tailored solutions.